Máy thổi màng 3 lớp
Áp dụng kỹ thuật của Đức, với kiểu thiết kế thông dụng và hệ thống hóa, ghép màng bởi 3 loại vật liệu có tính năng khác nhau, có thể thổi ra màng mỏng ghép với tính năng tổng hợp tốt. Máy có tính linh động tốt, chức năng đầy đủ, là sản phẩm lý tưởng thay thế cho máy thổi màng đơn hiện nay.
Sản phẩm: màng tiêu chuẩn, màng đóng gói chất lỏng, màng đơn, màng ghép đóng gói, màng ghép v.v…
Thông số kỹ thuật:
Kết cấu tổng thể máy chính: áp dụng kỹ thuật của Đức, sử dụng hộp giảm tốc truyền động, năng suất cao, hiệu quả định hình nguyên liệu cao. Bộ điều khiển điều chỉnh biến tần.
• 2 máy đùn chính SJ45/30, 01 máy đùn SJ50/30.
• Nguyên liệu thích hợp: LDPE, HDPE, LLDPE, EVA, LLDPE.
• Năng suất: Máy đùn SJ45/30 : 60 – 70 kg/giờ (LDPE); máy đùn SJ50/30 : 70 – 80 kg/giờ (LDPE).
• Đường kính trục vít : Φ 45 mm hoặc Φ 50 mm.
• Tỉ lệ đường kính và chiều dài: 1:30.
• Tốc độ trục vít: 135 vòng/phút.
• Động cơ khởi động: 22 kw (SJ45/30) và 30 kw (SJ50/30).
• Gia nhiệt xi lanh: 3 giai đoạn, đồ sứ gia nhiệt.
• Phương thức làm nguội xi lanh: làm nguội bằng gió.
• Đường kính khuôn: Φ 200 / 250 / 300 tự chọn.
• Đầu khuôn xoay vòng: kiểu xoay vòng liên tục hướng đơn.
• Dung lượng phễu chứa: 150 kg.
• Tốc độ dẫn kéo màng: 5 - 60 m/phút.
• Đường kính cuộn màng tối đa: Φ 800 mm.
• Chu vi tối đa của màng: 1.300 mm.
• Nguồn điện bên người sử dụng: 3 pha x 380 V; 50 Hz.
• Độ mỏng màng chênh lệch: < ± 8 %, độ bằng phẳng đầu màng: < ± 2 mm (theo tiêu chuẩn thổi màng 0,03 – 0,08 mm)
• Sản lượng: 100 kg/giờ – 120 kg/giờ.
• Chênh lệch chiều dài chu vi đường kính ngoài của cuộn màng: < ± 5 % (đường kính cuộn thu màng: < 300 mm.)
• Kích thước bề ngoài máy (dài x rộng x cao): 8.950 x 8.000 x 6.650 (mm)
• Máy nén 0,3 – 0,6 m3/phút
Ưu điểm thiết bị:
• Điều khiển tự động, lực cản thấp, nhiệt độ chảy màng phân chia đều đặn, có sản lượng lớn. • Thay lưới lọc bằng tay nhanh chóng. • Cảm biến khống chế nhiệt độ. • Trang bị màn hình hiển thị áp lực bên trong để kiểm tra áp lực nguyên liệu tan chảy trong xi lanh. • Bộ phận thu màng gồm bộ ly hợp bột từ khống chế lực căng màng mỏng, đảm bảo lực căng của cuộn màng được đồng bộ. | | 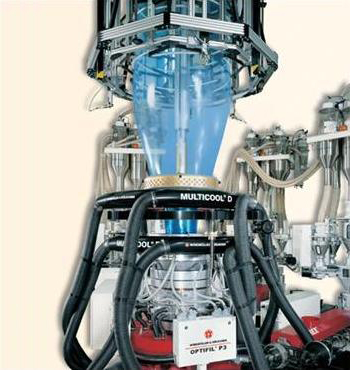 |
• Năng suất máy chính đạt tiêu chuẩn, hiệu quả định hình cao, lực căng thu màng và dẫn màng ổn định, phạm vi chỉnh rộng, thu màng ngay ngắn.
• Chế phẩm màng chia lớp rõ ràng, không có hiện tượng trộn lẫn nhau, màng không bị bong tróc.
Quy trình công nghệ sản xuất xi măng

Quá trình sản xuất xi măng được mô tả qua 3 giai đoạn cụ thể như sau:
1. Quá trình chuẩn bị nguyên nhiên liệu:
Từ mỏ, đá vôi được khai thác và vận chuyển về đổ qua máy đập búa (1) làm cho kích thước nhỏ hơn và đưa lên máy rải liệu (2) để chuyển vào kho (tạo nên tính đồng nhất sơ bộ cho nguyên liệu). Tương tự đất sét, quặng sắt, than đá và nguyên liệu khác cũng được đưa vào kho và đồng nhất theo cách trên.
Tại kho chứa, mỗi loại sẽ được máy cào liệu (5) và (6) cào từng lớp (đồng nhất lần hai) đưa lên băng chuyền để nạp vào từng bồn chứa liệu (7) theo từng loại đá vôi, đất sét, quặng sắt, thạch cao, than...
Than đá thô từ kho chứa sẽ được đưa vào máy nghiền đứng (20) để nghiền, với những hạt đạt yêu cầu sẽ được đưa vào bồn chứa (21) còn những hạt chưa đạt sẽ hồi về máy nghiền để nghiền lại. Việc khống chế kích thước sẽ đảm bảo hạt than nhiên liệu cháy hoàn toàn khi cấp cho đầu lò nung và tháp trao đổi nhiệt.
2. Quá trình sản xuất clinker thành phẩm:
Từ các bồn chứa liệu (7), từng loại nguyên liệu được rút ra và chạy qua hệ thống cân định lượng theo đúng tỷ lệ. Tất cả nguyên liệu sẽ được gom vào một băng tải chung và đưa vào máy nghiền đứng (8) để nghiền về kích thước yêu cầu, tại đây nguyên liệu đã được đồng nhất một lần nữa. Bột liệu sau khi nghiền được chuyển lên silo chứa liệu sống (9) chuẩn bị để cấp cho lò nung.
Lò nung (12) là một ống tròn đường kính từ 3 - 5 mét và dài từ 30 - 80 mét tùy vào công suất của lò. Góc nghiêng của lò từ 30 – 50 độ để tạo độ nghiêng cho dòng nguyên liệu chảy bên trong. Tại đầu ra của clinker sẽ có một dàn quạt thổi gió tươi làm nguội nhanh clinker.
Tháp phân giải (11) là một hệ thống gồm từ 3-5 tầng, mỗi tầng có 1 hoặc 2 ống lồng dạng chóp có cấu tạo để tăng thời gian trao đổi nhiệt của bột liệu. Bột liệu được cấp từ trên đỉnh tháp và đi xuống, nhiệt nóng từ than được đốt cháy từ tháp phân giải và lò nung đi lên sẽ tạo điều kiện cho phản ứng tạo khoáng bên trong bột liệu. Mặc dù bột liệu đi xuống và khí nóng đi lên nhưng thực chất quá trình này là trao đổi nhiệt cùng chiều do cấu tạo đặc biệt của các xyclon trao đổi nhiệt.
Than mịn được rút từ bồn chứa trung gian (21) cấp cho các béc phun ở tháp trao đổi nhiệt và đầu lò nung để được đốt cháy nung nóng bột liệu.
Bột liệu sống được rút ra từ silo chứa (9), qua cân định lượng và được đưa lên đỉnh tháp trao đổi nhiệt bằng thiết bị chuyên dùng. Từ trên đỉnh tháp (11), liệu từ từ đi xuống qua các tầng xyclon kết hợp với khí nóng từ lò nung đi lên được gia nhiệt dần lên khoảng 800-900oC trước khi đi vào lò nung (12). Trong lò, ở nhiệt độ 1.450oC các oxit CaO, SiO2, Al2O3, Fe2O3 có trong nguyên liệu kết hợp với nhau tạo thành một số khoáng chính quyết định chất lượng của clinker như: C3S, C2S, C3A và C4AF.
Viên clinker ra khỏi lò sẽ rơi xuống dàn làm lạnh (13), hệ thống quạt cao áp đặt bên dưới sẽ thổi gió tươi vào làm nguội nhanh viên Clinker về nhiệt độ khoảng 50 ÷ 90oC, sau đó clinker sẽ được chuyển lên silo chứa clinker.
3. Quá trình sản xuất xi măng: Clinker sẽ được rút từ Silo, cấp vào Bin chứa (15) để chuẩn bị nguyên liệu cho quá trình nghiền xi măng. Tương tự thạch cao và phụ gia từ kho cũng được chuyển vào bồn chứa riêng theo từng loại. Dưới mỗi bồn chứa, nguyên liệu được qua cân định lượng theo đúng khối lượng của đơn phối liệu, xuống băng tải chính đưa vào máy cán (16) để cán sơ bộ, sau đó được đưa vào máy nghiền xi măng (17). | |  |
Bột liệu ra khỏi máy nghiền được đưa lên thiết bị phân ly (18), tại đây những hạt chưa đạt yêu cầu sẽ được hồi lưu về máy nghiền để nghiền tiếp còn những hạt đạt kích thước yêu cầu được phân ly tách ra, đi theo dòng quạt hút đưa lên lọc bụi (19) thu hồi toàn bộ và đưa vào silo chứa xi măng (22). Quá trình nghiền sẽ diễn ra theo một chu trình kín và liên tục.
Máy rửa cát
 | | Máy rửa cát là thiết bị không thể thiếu trong quá trình sản xuất cát bằng nước nhằm nâng cao chất lượng sản phẩm cát. Chức năng của máy là làm sạch hỗn hợp cát được cấp vào từ thiết bị sản xuất cát và được sử dụng rộng rãi trong công nghiệp sản xuất vật liệu xây dựng, nhà máy cát sỏi, thủy tinh, sản xuất bê tông, khu khai thác cát, trạm trộn xi măng, nhà máy thủy điện… |
Nguyên lý làm việc:
Thông thường, cát có chứa tạp chất và bột đá. Máy rửa cát thực hiện nhiệm vụ loại bỏ các tạp chất. Các máy rửa cát có hệ thống guồng quay nhiều cánh, quay tròn liên tục trong rãnh nước tiến hành đảo trộn cát với dòng nước chảy qua, tốc độ quay của bánh quay được điều khiển thông qua tốc độ động cơ. Như vậy, các tạp chất lẫn trong cát sẽ được loại bỏ và cát sạch được tách loại nước đưa ra ngoài.
Thông số kỹ thuật:
• Kích thước guồng quay (dài × rộng): Φ 3.000 × 1.600 mm.
• Tốc độ guồng quay: 1.179 vòng/phút.
• Năng suất: 50 ~ 120 tấn/giờ.
• Kích thước liệu nạp: ≤10 mm.
• Lượng nước tiêu thụ: 70 ~ 120 m3.
• Công suất động cơ: 15 Kw.
• Model bộ giảm tốc: ZQ65-50-I-Z.
• Kích thước ngoài (dài x rộng x cao): 3.845 × 3.000 × 3.080 mm.
Ưu điểm công nghệ/thiết bị: • Máy rửa cát có cấu trúc đơn giản, kết cấu hợp lý, độ bền cao. • Vận hành và bảo trì dễ dàng. • Năng suất cao, chất lượng cát sau rửa tốt. • Tiết kiệm nước, thân thiện với môi trường. | |  |
STINFO Số 7/2014
Tải bài này về tại đây.