Nếu các tòa nhà trong thành phố nối với nhau bằng những con đường, thì trong một sản phẩm điện tử, các linh kiện cũng được kết nối nhờ các vi mạch trên bo mạch. Những năm 1950, người ta dùng công nghệ xuyên lỗ để lắp ráp linh kiện điện tử lên một bo mạch (BM). Theo đó, bề mặt BM được khoan lỗ. Linh kiện điện tử có chân được cắm xuyên qua lỗ, bẻ gấp chân vào và hàn lại ở mặt bên kia, có thể thực hiện hoàn toàn thủ công hoặc dùng cánh tay robot giả lập thao tác con người.
Đến thập niên 1980, xuyên lỗ vẫn là công nghệ phổ biến trong lắp ráp điện tử nhưng tồn tại một số nhược điểm. Kích thước và hình dạng linh kiện khác nhau nên quy trình cắm cần trật tự cố định, đòi hỏi công nhân phải giàu kinh nghiệm. Chân linh kiện bẻ gấp tạo mối nối tốt nhưng khó tháo ráp. Mối hàn khá to, nếu khoảng cách giữa các mối hàn quá gần dễ bị dính nhau, ngược lại thì BM trở nên to và đắt tiền.
Để đáp ứng yêu cầu đặt ra cho BM thế hệ mới là: càng nhỏ, càng rẻ và càng tốt, từ sau năm 1980, công nghệ dán bề mặt (SMT - Surface Mount Technology) hay còn gọi là công nghệ hàn linh kiện bề mặt ra đời, thay thế phương pháp xuyên lỗ và trở thành xu hướng mới trong lắp ráp linh kiện điện tử.
SMT – Công nghệ dán bề mặt
SMT là công nghệ lắp ráp linh kiện điện tử bằng cách dán trực tiếp linh kiện lên bề mặt BM mà không cần khoan lỗ.
Linh kiện dùng cho công nghệ SMT gọi là linh kiện dán - SMD (Surface Mount Device). Bất cứ linh kiện xuyên lỗ nào cũng có linh kiện dán tương ứng. SMD nhỏ và nhẹ, cố định lên BM bằng một chấm kem hàn rất nhỏ, cho phép tăng mật độ và độ phức tạp của các vi mạch trên BM nhiều lần.
Khi thế hệ linh kiện điện tử to cũ bị thay thế bởi những con chip chỉ nhỏ bằng 1/10 hạt gạo thì công nghệ SMT cũng “soán ngôi” công nghệ xuyên lỗ nhờ tính năng ưu việt của nó:
• Ưu điểm đầu tiên, dễ thấy nhất của SMT là không cần khoan lỗ BM.
• Quá trình tự động hóa cao, có thể tự hiệu chỉnh những lỗi nhỏ gặp phải.
• Có thể gắn linh kiện lên cả hai mặt BM.
• Bền hơn so với xuyên lỗ, đặc biệt trong điều kiện bị rung, lắc, va đập với cường độ không quá cao.
• Giá linh kiện dán rẻ hơn linh kiện xuyên lỗ.
• Năng suất cao và rất linh động khi thay đổi model BM.
• Ưu điểm lớn nhất của SMT vẫn là chế tạo được BM nhỏ gọn với cấu trúc vi mạch phức tạp. Tuy nhiên, đây cũng là nhược điểm bởi BM quá nhỏ nên khó thao tác hơn.
Nhờ điều khiển, xử lý bằng máy tính hiện đại, các máy SMT ngày nay đảm bảo quá trình tự động hóa cao, sai sót cực nhỏ, giảm chi phí lao động và tăng năng suất đáng kể. Kích thước và trọng lượng BM nhỏ hơn từ 2 đến 5 lần so với loại xuyên lỗ, và giảm từ ¼ đến hơn một nửa chi phí vật liệu. Mặt khác, nếu so sánh năng suất của một máy xuyên lỗ tự động là 12.000 linh kiện/giờ và một máy SMT gia công trên 42.000 linh kiện/giờ với sự chính xác gần như tuyệt đối, có thể hình dung SMT như một công nghệ “hái ra tiền”.
Một số ít trường hợp vẫn cần đến phương pháp xuyên lỗ, chủ yếu dùng cho linh kiện kích thước lớn, thường xuyên chịu áp lực cơ học, có điện áp cao, cần tháo lắp liên tục…Tùy thiết kế BM, người ta có thể chọn lựa giữa xuyên lỗ và SMT, hoặc kết hợp cả hai phương pháp.
Sơ lược về công nghệ SMT
Nhìn chung, quá trình dán linh kiện lên BM bằng công nghệ SMT gồm 4 bước cơ bản:
1. Quét kem hàn (Solder Paste) lên bề mặt BM ở vị trí cần gắn linh kiện. Kem hàn quét qua lỗ của một mặt nạ kim loại (metal mask hoặc stencil) được đặt trên BM để tránh dính vào nơi không mong muốn (lỗ trên mặt nạ kim loại được đục thủng ở ngay vị trí cần dán của BM). Kem hàn có dạng bột nhão, tính bám dính cao, thành phần thay đổi tùy công nghệ và đối tượng hàn. Sau đó, BM chuyển sang máy gắn linh kiện.
2. Gắn linh kiện. Máy gắn linh kiện tự động gỡ linh kiện từ băng chuyền hoặc khay và đặt vào vị trí tương ứng đã được quét kem hàn. Sau khi sấy khô nhanh kem hàn bằng nhiệt hoặc tia UV, BM được lật mặt và quá trình gắn lặp lại. Khi hoàn tất cả hai mặt, BM chuyển sang lò sấy. Công nghệ SMT mới còn cho phép gắn linh kiện cùng lúc cả hai mặt
3. Gia nhiệt. Tại lò sấy, BM đi qua các khu vực với nhiệt độ tăng dần để linh kiện có thể thích ứng. Ở nhiệt độ đủ lớn, kem hàn nóng chảy, dán chặt linh kiện lên BM. BM sau đó được rửa bằng một số hóa chất, dung môi và nước để làm sạch vật liệu hàn rồi dùng khí nén làm khô nhanh.
4. Kiểm tra và sửa lỗi sản phẩm.
Khó khăn khi ứng dụng vào sản xuất là SMT đòi hỏi sự chính xác tuyệt đối và trình độ quản lý cao trong quá trình gia công. Đầu tư ban đầu cho máy móc thiết bị cũng tương đối lớn và mất nhiều thời gian, bởi kích thước linh kiện quá nhỏ, nếu quá trình tự động hóa không đạt chuẩn sẽ gây sai sót lớn và tốn chi phí.
SMT trên thế giới
Theo cơ sở dữ liệu tiếp cận được, sáng chế (SC) đầu tiên về SMT đăng ký năm 1976 nhưng đến năm 1980 SMT mới bắt đầu phổ biến. IBM tiên phong ứng dụng SMT trong lĩnh vực máy tính. Lúc này, phương pháp xuyên lỗ vẫn được ưa chuộng do dễ hàn và tháo lắp. Hạn chế của chất lượng BM cũng khiến SMT khó phát triển. Sự ra đời của BM chất lượng cao đã mở rộng thị trường cho SMT từ sau năm 2000.
Do liên hệ chặt chẽ với ngành điện tử, những năm 2008, lĩnh vực SMT chịu ảnh hưởng không nhỏ của cuộc khủng hoảng kinh tế toàn cầu với số lượng SC sụt giảm khá mạnh. Tuy nhiên, theo báo cáo gần đây của Electronics. CA. Publications, thị trường SMT đang hồi phục cùng với sự khởi sắc của nền kinh tế, nhanh chóng thay thế công nghệ xuyên lỗ nhờ đột phá về năng suất và độ tin cậy.
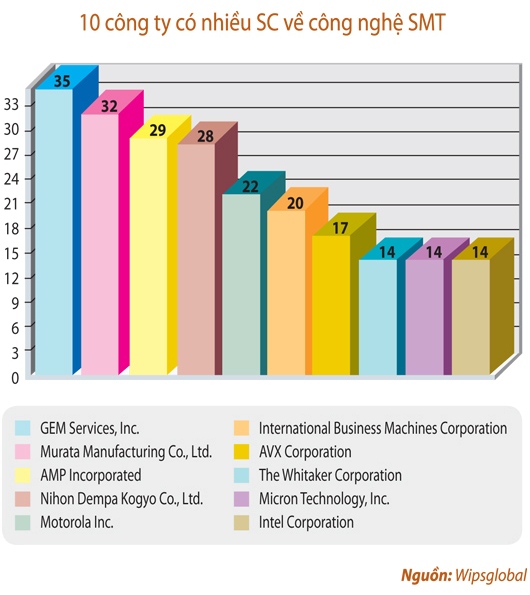
Tính đến nay, gần 1.300 SC về SMT trên thế giới hầu hết đăng ký tại Mỹ. Nhiều SC nhất thuộc về những công ty sản xuất và cung cấp linh kiện điện tử hàng đầu. Trong top 10, đến 8 công ty có trụ sở chính tại Mỹ (AMP Incorporated, Motorola, IBM, AVX, The Whitaker, Micron Technology, Intel), còn lại của Nhật (Murata, Nihon Dempa Kogyo) và Anh (GEM Services).
Phân tích theo phân loại SC quốc tế IPC cho thấy 3 hướng nghiên cứu chính về SMT: 19% SC về thiết bị mạch tích hợp (H01L); 16% SC về màng phim kỹ thuật để sản xuất BM (H05K); khoảng15 % SC về hệ thống phân phối điện (H01R). Một số hướng nghiên cứu khác là về phương pháp và thiết bị hàn, hợp kim hàn, ứng dụng SMT trong thiết bị truyền thông, biến áp...
Và tại Việt Nam
Chậm chân hơn các nước khác một chút, tại Việt nam, công nghệ SMT chỉ bắt đầu “sôi động” trong ngành điện tử từ năm 2008. Một số nhà cung cấp thiết bị SMT tại nước ta hiện nay có: SMT Vietnam, Siemens, Panasonic, Fuji, Samsung, Matsushita…
Do chi phí đầu tư quá cao, nên thời gian đầu, đa số công ty trong nước chọn cách hợp tác chuyển giao công nghệ, học hỏi mô hình quản lý từ tập đoàn nước ngoài. Công ty Cổ phần Bóng đèn Điện Quang là một trong những doanh nghiệp nội địa áp dụng SMT thành công trong sản xuất. Sản phẩm ballast cho đèn compact dùng công nghệ SMT nhỏ gọn, ít tỏa nhiệt và tăng tuổi thọ thiết bị.
Tháng 10 vừa qua, triển lãm lần thứ 5 về công nghiệp phụ trợ do Tổ chức Xúc tiến Thương mại Nhật Bản (JETRO) và Trung tâm Xúc tiến Thương mại và Đầu tư (ITPC) tổ chức đã giới thiệu một số dây chuyền SMT công nghệ cao phục vụ ngành điện tử. Theo TS. Trần Quang Hùng – Tổng thư ký Hiệp hội Doanh nghiệp Điện tử Việt Nam (VEIA), ngành công nghiệp sản xuất linh phụ kiện điện tử Việt Nam phát triển mạnh mẽ từ năm 2011 và hứa hẹn sẽ tăng gấp đôi doanh thu mỗi năm. Ứng dụng hiệu quả SMT trong sản xuất sẽ góp phần đáng kể vào lợi ích quốc gia nhờ giảm chi phí nhập khẩu, nâng cao hiệu quả sản xuất và giá trị sản phẩm.
Minh Nhật, STINFO Số 12/2012